|
1¡¢ A brief introduction to the constitutive model of dynamic mechanics
The constitutive model analysis software of dynamic mechanics is a customized professional simulation and analysis tool to solve the problems of electric, magnetic, thermal, structural and other multi field coupling in dynamic mechanics. The software was originally developed by Archimedes, whose core value lies in the parameterized grid model and customized analysis process.
2¡¢ Key techniques of constitutive model in dynamic mechanics
1. Material constitutive model: specific elastic model, elastic-plastic model, Johnson cook model, zerilli Armstrong model, Steinberg Guinan model, HJC, RHT model. The constitutive model describes the material's own properties, which can reflect the physical properties of the material in the process of processing deformation, and also can reflect the thermodynamic dynamic characteristics of the material. The constitutive model reflects the functional relationship between stress and temperature, strain and strain rate. Temperature change, workpiece deformation speed and deformation degree have a great influence on flow stress. Small changes can cause significant changes in flow stress. In an ideal state, the measurement standard of material constitutive model is the description of physical properties such as work hardening behavior, strain rate sensitivity, temperature sensitivity, strain / strain rate, etc. at present, it is extremely difficult to fully meet this standard. Many researchers only consider strain rate sensitivity, plastic deformation and other factors, but it is difficult to explain clearly in the process of theoretical formula solving. Considering these factors, the constitutive model constructed by experiments is widely used in practical engineering. 2. In the process of dynamic mechanics, there is contact between the impact body and the workpiece, even between the workpiece and the debris. If there is contact, there will be friction. Therefore, a correct friction model plays an important role in the finite element simulation. In mechanics, the contact friction problem is a very complex problem, which reflects the highly nonlinear boundary conditions. To study the contact friction problem, we need to determine the movement mode of the object before contact and the interaction of the object after contact, and also deal with the friction and heat transfer between the contact surfaces of the workpiece. 3. The separation criteria can be roughly divided into geometric criteria and physical criteria. The former depends on the change of geometric dimension, while the latter mostly takes the critical value of relevant physical quantities as the criterion. A reasonable chip separation criterion, whose value should be independent of the change of cutting conditions after material selection, accurately reflects the physical and mechanical properties of workpiece materials in cutting. 4. In quasi-static analysis or some dynamic analysis, in order to improve the efficiency of finite element simulation analysis, the method of mass scaling is often used.
There are two methods of mass scaling in display dynamic analysis: constant mass scaling and variable mass scaling. The two methods can be used separately or in combination. Mass scaling can be used for the entire model, or for cell groups.
3¡¢ Constitutive model of dynamic mechanics
material behavior under dynamic loading 2 material model provided by engineering data 3 material deformation 4 principal stress 5 elastic response 6 nonlinear response 7 effective material model in explicit dynamic analysis 8 elastic constant 9 physical and thermal properties 10 linear elastic model 10.1 isotropic elastic model 10.2 orthotropic elastic model 10.3 viscoelastic model 11 superelastic model 12 plasticity 12.1 plasticity overview 12.2 bilinear isotropic hardening / bilinear follow-up hardening model 12.3 multilinear isotropic hardening / multilinear follow-up hardening model 12.4 Johnson cook strength model 12.5 Cowper Symonds strength model 12.6 Steinberg Guinan strength model 12.7 zerilli Armstrong strength model 13 brittle / granular material model 13.1 Drucker Prager strength model 13.2 Johnson Holmquist strength model 13.2.1 Johnson Holmquist smooth transition strength model (jh2) 13.2.2 Johnson Holmquist segmental strength model (jh1) 13.3 strength model of RHT concrete 13.4 Mo granular strength model Equation of state 14.1 equation of state of ideal gas 14.2 properties of equation of state 14.3 equation of state in Mei Gruneisen form 14.4 polynomial equation of state 14.5 equation of impact state 14.6 high energy explosives 15 porous material model 15.1 porous material model overview 15.2 crush the foam material. 15.3 linear compression equation of state 15.4 nonlinear compression equation of state 15.5 p-alpha equation of state 16 failure model 11 overview of material failure 12 plastic strain failure model 13 main stress / strain failure model 14 random failure model 15 failure model of tensile pressure 16 crack softening failure model 17 Johnson cook failure model 18 Grady spallation failure model
4¡¢ Examples of finite element simulation analysis
1. Explosion process of fragment warhead (based on electric explosion test)
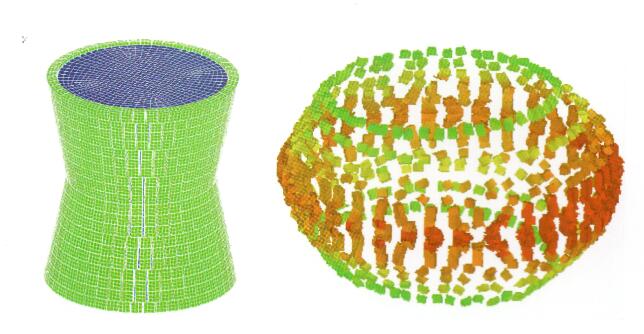
2. Simulation of armor piercing projectile penetrating target process (based on electromagnetic gun impact and Hopkinson rod test)
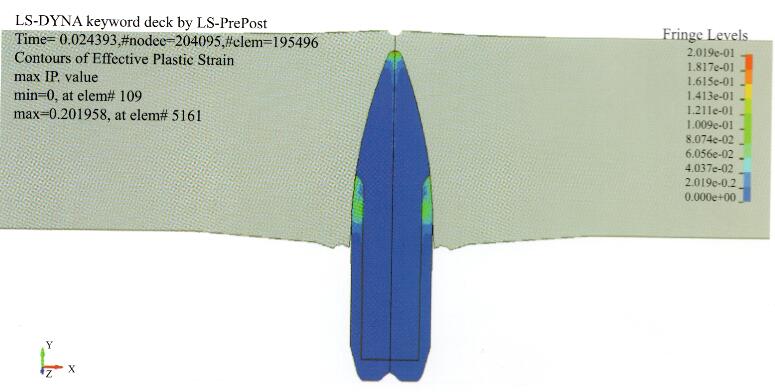
3. Simulation of the action process of human body and air bag (based on electric explosion test)
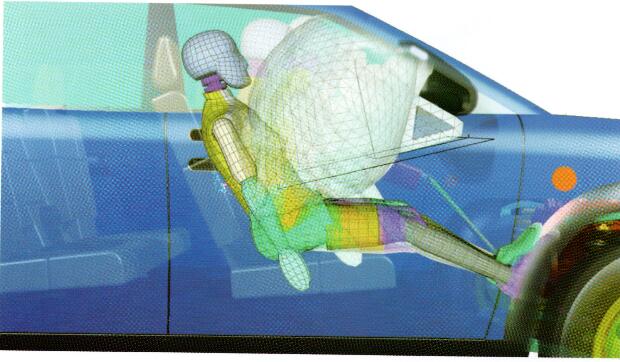
4. Vehicle collision simulation (dynamic structure Hopkinson test as the experimental basis)
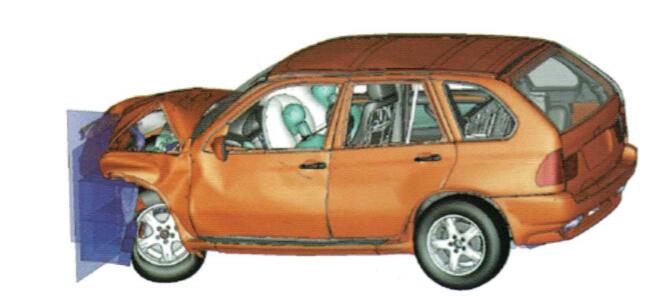
5. Simulation of long bar impact process (based on Taylor bar and Hopkinson bar test)
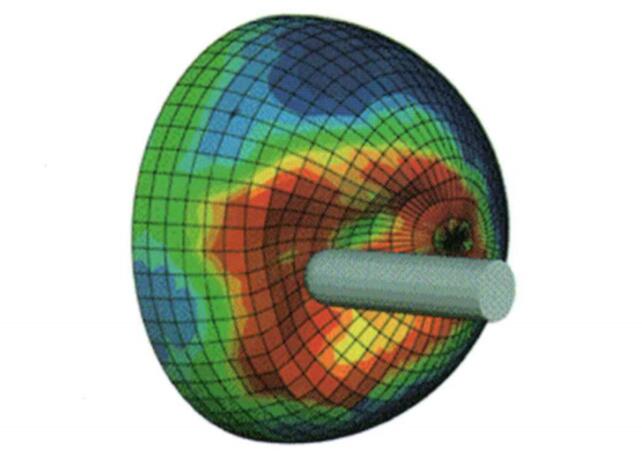
6. Propagation simulation of explosion shock wave (based on electric explosion test)
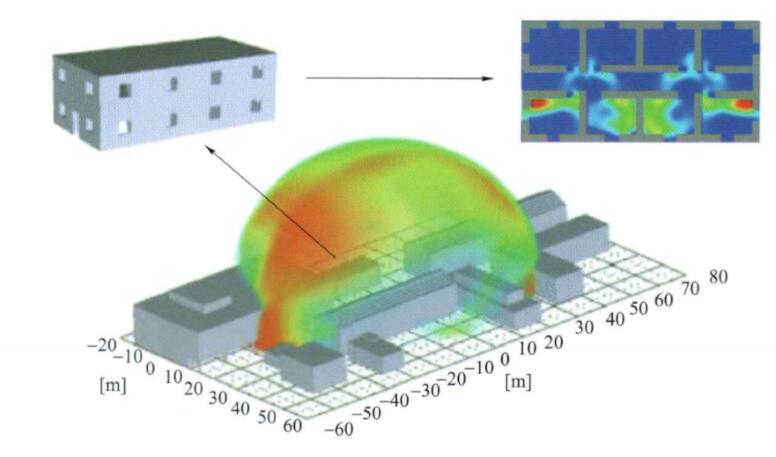
7. Hypervelocity impact simulation (based on Electromagnetic Railgun)
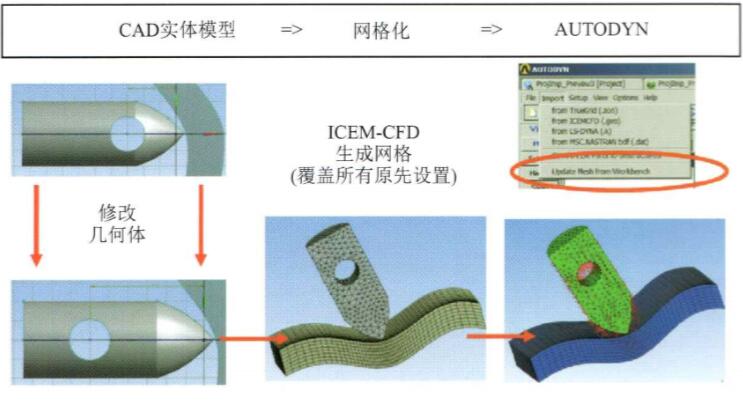
|